Share this
Building Better, Faster, Lighter
by Sean Hill on Jul 16, 2025
How offsite manufacturing is reshaping sustainable architecture
At RISE Design Studio, we’re constantly reimagining what building can be. Not just aesthetically, but environmentally and ethically. We believe that to meet today’s challenges, we can’t keep relying on yesterday’s methods. That’s where offsite manufacturing (OSM) and modular construction enter the story—not as buzzwords, but as powerful shifts in how we shape space.
Modular isn’t just a method. It’s a mindset. A decision to plan better, waste less, and design buildings that serve both people and planet.
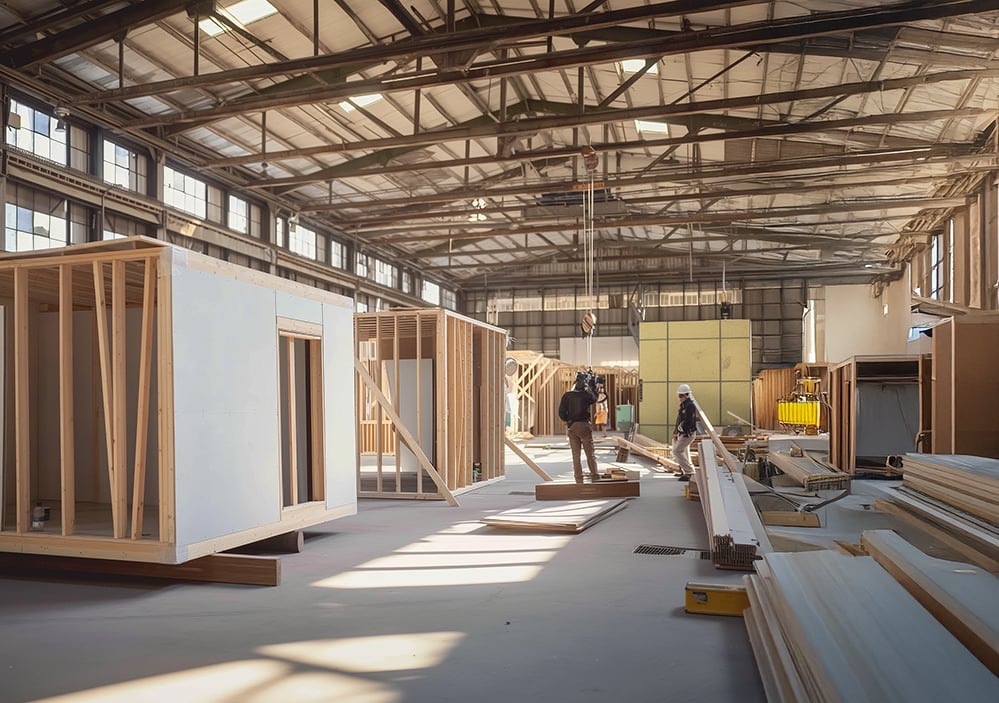
Precision-crafted modules taking shape in a controlled factory environment — a key step in delivering low-energy, high-quality homes through offsite construction.
What Exactly Is Offsite Manufacturing?
Offsite manufacturing flips the traditional building process on its head.
Rather than erecting walls brick by brick in unpredictable conditions, we create elements—walls, floors, entire volumetric pods—in purpose-built factories where every joint, seal, and detail is crafted in a climate-controlled environment. These precision-made parts are then transported and assembled on-site, slotting into place like a perfectly rehearsed performance.
It’s architecture with foresight.
It’s not cutting corners—it’s refining them.
From complex commercial builds to finely detailed homes, OSM is proving itself on projects of every scale. And as the technology matures, it’s no longer just for high-rises or housing estates—it’s available to individual homeowners who want to build consciously.
Building in a City That’s Running Out of Time
London’s housing shortfall is no secret. The demand for homes—high-quality, comfortable, low-energy homes—far outpaces supply. Since 2015, only a fraction of the GLA’s housing targets have been met. But this isn’t just about numbers on a spreadsheet. It’s about people waiting years for a place to call their own.
The reasons for the shortage are layered—funding, land availability, bureaucracy—but the way we build is one we can change.
We believe modular design, when combined with low-embodied carbon materials and energy-efficient detailing, has the power to help shift this imbalance.
Because speed matters. But so does quality. And sustainability is non-negotiable.
The Sustainability Edge
There’s a misconception that modular means cheap, cookie-cutter, uninspired. We reject that.
At RISE, we’re crafting buildings that reduce operational energy by up to 75%, that filter air for well-being, that adapt to changing needs. OSM, particularly when paired with timber-based systems like CLT, can significantly lower a project’s embodied carbon. It’s not just about how a home performs after it's built—it’s about how responsibly it came into being.
→ Precision cutting means less waste
→ Closed-panel systems improve airtightness and reduce heating demand
→ Factory conditions improve working safety and allow better materials management
→ Shorter site times mean fewer deliveries, fewer emissions, less disruption
This is design for the long game.
Why Modular Is a Smart Response for Urban Living
London plots are tight. Access is tricky. Neighbours are close. OSM simplifies the logistics. While the groundworks are being prepared, the building is taking shape in the factory. When it arrives, the structure can be craned into place in a matter of days rather than months.
→ Faster builds mean lower prelim costs (think: scaffolding, security, facilities)
→ Tighter programmes mean fewer delays, fewer surprises
→ Reduced site time means happier neighbours (and clients)
And once built, these homes perform. They’re warm, they’re quiet, they’re easy to maintain. They’re the opposite of throwaway.
Designing for Repetition Without Repetition
There’s a skill to designing modular buildings that don’t feel modular. That don’t scream system-built. We do this by starting with the human experience—light, movement, texture, proportion. Then we look at repetition not as compromise, but as opportunity.
By standardising certain elements—bathroom cores, kitchen layouts, window sizes—we can free up the budget to invest elsewhere: sustainable materials, landscaping, passive cooling strategies. The goal is not to impose a system but to work creatively within it.
→ A modular structure can still have character
→ A modular home can still be crafted
→ Repetition can make room for poetry
Limitations We Can Design Around
No building method is perfect.
OSM does require early-stage decisions. Flexibility on-site is limited, so coordination and tolerance planning must be meticulous. Integrating new modules with existing buildings can be tricky, and supply chains for larger prefabricated elements in the UK still lag behind mainland Europe.
There are also public perceptions to challenge—assumptions that prefab equals poor quality. But this is changing. The industry is evolving. And clients, when shown the benefits, are responding.
The key is transparency. Design integrity. And a commitment to craftsmanship, regardless of how or where that craft takes place.
A Platform for Innovation
Imagine a future where buildings arrive like beautifully wrapped parcels—solar-ready, airtight, breathable, and adaptable. Where modular units can be relocated, expanded, reused. Where homes are demountable, not disposable.
That future isn’t far off. It just needs enough of us to believe in it—and to start building towards it.
The potential for offsite methods goes far beyond speed and cost. It’s about a complete shift in how we think about making architecture: as something that can be both industrial and intimate, repeatable and personal, efficient and enduring.
Final Word: Why We’re Leaning In
At RISE, we believe that modular construction is not a compromise—it’s an evolution. Used well, it gives us a pathway to more sustainable cities, more affordable homes, and more adaptable futures.
We don’t treat modular builds as separate from the rest of our work. They still go through the same process of listening, of context reading, of spatial choreography. They are still guided by our belief in beauty, simplicity, and sustainability.
If we want to build homes that are worthy of tomorrow, we need to build them better today.
Building Lightly with Purpose
At RISE, modular and offsite construction isn’t just a method — it’s part of a bigger mission. A mission to design buildings that are deeply thoughtful, beautifully made, and fundamentally sustainable.
Whether we’re designing a single-family home or a series of modular dwellings, our approach stays the same:
→ Prioritise low-energy use
→ Reduce embodied carbon
→ Maximise natural light, comfort, and adaptability
→ Design spaces that honour people and planet
This isn’t about building faster just for the sake of speed. It’s about building better — with care, craft, and future generations in mind.
Curious about modular construction, sustainable materials, or how offsite might work for your project?
Let’s explore how to design a home that’s ready for tomorrow — and rooted in purpose.
→ Email us: architects@risedesignstudio.co.uk
→ Call us: 020 3947 5886
RISE Design Studio: Architects, Interior Designers and Sustainability Experts
Company Reg No: 08129708 – VAT No: GB158316403
© RISE Design Studio. Trading since 2011.
Share this
- Architecture (151)
- Sustainable architecture (138)
- Design (67)
- Passivhaus (67)
- Sustainable Design (65)
- Retrofit (57)
- London (51)
- New build (51)
- Renovation (43)
- energy (39)
- interior design (37)
- Building materials (34)
- Planning (33)
- Environment (31)
- climate-change (30)
- Inspirational architects (27)
- Refurbishment (27)
- enerphit (27)
- extensions (27)
- Building elements (22)
- Inspiration (21)
- Rise Projects (16)
- Extension (15)
- Innovative Architecture (14)
- London Architecture (13)
- net zero (13)
- Carbon Zero Homes (12)
- General (12)
- Philosophy (12)
- RIBA (11)
- Working with an architect (11)
- sustainable materials (11)
- architects (10)
- low energy home (10)
- Awards (9)
- Sustainable (9)
- Residential architecture (8)
- architect (8)
- Planning permission (7)
- Sustainable Architect (7)
- Airtightness (6)
- Eenergy efficiency (6)
- Passive house (6)
- Uncategorized (6)
- Virtual Reality (6)
- low carbon (6)
- BIM (5)
- Basement Extensions (5)
- Costs (5)
- RISE Sketchbook Chronicles (5)
- cinema design (5)
- construction (5)
- local materials (5)
- sustainable building (5)
- ARB (4)
- BIMx (4)
- Carbon Positive Buildings (4)
- Feasibility Study (4)
- Home extensions (4)
- House cost (4)
- Overheating (4)
- concrete (4)
- constructioncosts (4)
- insulation (4)
- modular architecture (4)
- mvhr (4)
- natural materials (4)
- structural (4)
- structuralengineer (4)
- working from home (4)
- Backland Development (3)
- Building in the Green Belt (3)
- Chartered architect (3)
- Home improvement (3)
- Paragraph 84 (3)
- Permitted development (3)
- Property (3)
- Spain (3)
- Sustainable Interiors (3)
- Sustainable Tennis Pavilion (3)
- Timber Structures (3)
- backland (3)
- circular economy (3)
- country house (3)
- countryside (3)
- furniture (3)
- listed buildings (3)
- plywood (3)
- sustainability (3)
- sustainable structure (3)
- zero waste (3)
- 3D models (2)
- AECB (2)
- Architects in Spain (2)
- Artificial Intelligence (AI) (2)
- BREEAM (2)
- Bespoke lighting (2)
- Bricks (2)
- Building energy (2)
- Chartered Practice (2)
- Commercial Architecture (2)
- Contractor (2)
- Covid-19 (2)
- Ecohouse (2)
- Fees (2)
- Furniture design (2)
- Garden studio (2)
- Heat Pumps (2)
- Heritage (2)
- Japanese Archiecture (2)
- Loft conversion (2)
- Mews House Retrofit (2)
- Modern Methods of Construction (2)
- Paragraph 79 (2)
- Paragraph 80 (2)
- Period Homes (2)
- Permitted development rights (2)
- Recycling (2)
- Roof extension (2)
- Social Distancing (2)
- Social housing (2)
- Store Design (2)
- Sustainable Affordable Homes (2)
- Sustainable Extensions (2)
- Tennis Pavilion (2)
- Timber Construction (2)
- Welbeing (2)
- ashp (2)
- barcelona (2)
- building information modelling (2)
- building regulations (2)
- co-working (2)
- design&build (2)
- epc (2)
- glazed-extensions (2)
- green architecture (2)
- greenbelt (2)
- health and wellbeing (2)
- historic architecture (2)
- house extension (2)
- interiorfinishes (2)
- light (2)
- living space (2)
- london landmarks (2)
- londoncinemas (2)
- openingupworks (2)
- peter zumthor (2)
- project management (2)
- rammed earth (2)
- renewable energy (2)
- self build (2)
- traditional (2)
- trialpits (2)
- waste (2)
- wooden furniture (2)
- #NLANetZero (1)
- 3D Printing (1)
- 3D Walkthroughs (1)
- Adobe (1)
- Alvar (1)
- Architect Barcelona (1)
- Architecture Interior Design (1)
- Architraves (1)
- Area (1)
- Art (1)
- Audio Visual (1)
- Balconies (1)
- Biodiversity (1)
- Biophilic Design (1)
- Birmingham Selfridges (1)
- Boat building (1)
- Boats (1)
- Brass (1)
- Brexit (1)
- Brownfield Development (1)
- Brutalist Architecture (1)
- Carpentry (1)
- Casting (1)
- Chailey Brick (1)
- Community Architecture (1)
- Concrete Architecture (1)
- Copper (1)
- Cornices (1)
- Cowboy Builders (1)
- Czech Republic, (1)
- Data Centers (1)
- David Lea (1)
- Designing with Stone (1)
- Dormer extension (1)
- EnvironmentalArchitecture (1)
- Flooding (1)
- Future of Housing (1)
- Gandhi memorial museum (1)
- Georgian Extension (1)
- Green Register (1)
- Green infrastructure (1)
- GreenDesign (1)
- History (1)
- India (1)
- Jan Kaplický (1)
- Japandi (1)
- Joinery (1)
- Kitchen Design (1)
- L-shaped dormer (1)
- Land value (1)
- Lord's Media Centre (1)
- Mapping (1)
- Marseilles (1)
- Mary Portas (1)
- Metal (1)
- Micro Generation (1)
- Mid Century Retrofit (1)
- Monuments (1)
- Mouldings (1)
- Mycelium Architecture (1)
- NPPF (1)
- Nature (1)
- New Build House (1)
- Office to Homes (1)
- Office to Hotel Conversion (1)
- Offsite manufacturing (1)
- Padel Court (1)
- Party Wall Surveyor (1)
- PeopleFirstDesign (1)
- Place (1)
- Podcast (1)
- Porch (1)
- Prefab (1)
- Procurement (1)
- RISE Team (1)
- Rebuild (1)
- Replacement Dwelling (1)
- ResilientFuture (1)
- Richard Rogers (1)
- Rural New Build (1)
- Sand (1)
- Scandinavian architecture (1)
- Selfbuild (1)
- Skirting (1)
- Small Sites Development (1)
- Solar Shading (1)
- Steel (1)
- Stone Architecture (1)
- Surveying (1)
- Sustainable Architect Fees (1)
- Sustainable Architect London (1)
- Sustainable Basement Extension (1)
- Sustainable Lighting (1)
- Sustainable Mews House (1)
- Sustainable Padel Court (1)
- Sverre fehn (1)
- VR (1)
- West london (1)
- Wildlife (1)
- Wood (1)
- architect fees (1)
- architectural details (1)
- arne jacobsen (1)
- avant garde (1)
- basements (1)
- brentdesignawards (1)
- building design (1)
- built environment (1)
- carbonpositive (1)
- cement (1)
- charles correa (1)
- charles eames (1)
- charlie warde (1)
- charteredarchitect (1)
- climate (1)
- climate action (1)
- codes of practice (1)
- collaboration (1)
- covid (1)
- dezeenawards (1)
- drone (1)
- eco-living (1)
- emissions (1)
- finnish architecture (1)
- foundations (1)
- futuristic (1)
- georgian architecture (1)
- glazed envelope (1)
- good working relationships (1)
- green building (1)
- hampstead (1)
- happiness (1)
- home extension (1)
- homesurveys (1)
- imperfection (1)
- independentcinemas (1)
- innovation (1)
- inspirational (1)
- internal windows (1)
- jean prouve (1)
- kindness economy (1)
- kintsugi (1)
- landscape architecture (1)
- lime (1)
- local (1)
- lockdown (1)
- mansard (1)
- manufacturing (1)
- materiality (1)
- modern architecture (1)
- moderninst (1)
- modernism (1)
- moulded furniture (1)
- natural (1)
- natural cooling (1)
- natural light (1)
- nordic pavilion (1)
- northern ireland (1)
- palazzo (1)
- placemaking (1)
- planningpermission (1)
- plywood kitchen (1)
- post-Covid (1)
- poverty (1)
- powerhouse (1)
- preapp (1)
- preapplication (1)
- ray eames (1)
- reclaimed bricks (1)
- recycle (1)
- reuse (1)
- ricardo bofill (1)
- risedesignstudio (1)
- rooflights (1)
- room reconfiguration (1)
- rural (1)
- satellite imagery (1)
- selfbuildhouse (1)
- shared spaces (1)
- site-progress (1)
- solarpvs (1)
- space (1)
- stone (1)
- structuralsurvey (1)
- sun tunnel (1)
- terraces (1)
- thegreenregister (1)
- totality (1)
- wabi-sabi (1)
- August 2025 (11)
- July 2025 (23)
- June 2025 (9)
- May 2025 (22)
- April 2025 (16)
- March 2025 (8)
- February 2025 (12)
- January 2025 (6)
- December 2024 (6)
- November 2024 (8)
- October 2024 (5)
- September 2024 (3)
- August 2024 (2)
- July 2024 (2)
- June 2024 (2)
- May 2024 (1)
- April 2024 (1)
- March 2024 (1)
- February 2024 (1)
- January 2024 (3)
- November 2023 (1)
- October 2023 (5)
- September 2023 (7)
- August 2023 (7)
- July 2023 (6)
- June 2023 (8)
- May 2023 (14)
- April 2023 (11)
- March 2023 (8)
- February 2023 (6)
- January 2023 (5)
- December 2022 (3)
- November 2022 (3)
- October 2022 (3)
- September 2022 (3)
- July 2022 (2)
- June 2022 (1)
- May 2022 (1)
- April 2022 (1)
- March 2022 (1)
- February 2022 (2)
- January 2022 (1)
- November 2021 (1)
- October 2021 (2)
- July 2021 (1)
- June 2021 (1)
- May 2021 (1)
- April 2021 (1)
- March 2021 (1)
- February 2021 (1)
- January 2021 (2)
- December 2020 (1)
- November 2020 (1)
- October 2020 (1)
- September 2020 (2)
- August 2020 (1)
- June 2020 (3)
- April 2020 (3)
- March 2020 (2)
- February 2020 (3)
- January 2020 (1)
- December 2019 (1)
- November 2019 (2)
- September 2019 (1)
- June 2019 (1)
- April 2019 (2)
- January 2019 (2)
- October 2018 (1)
- September 2018 (1)
- August 2018 (2)
- July 2018 (1)
- March 2018 (1)
- February 2018 (2)
- December 2017 (1)
- September 2017 (1)
- May 2017 (1)
- January 2017 (1)
- December 2016 (1)
- November 2016 (1)
- September 2016 (1)
- August 2016 (2)
- June 2016 (2)
- May 2016 (1)
- April 2016 (1)
- December 2015 (1)
- October 2015 (1)
- September 2015 (1)
- August 2015 (1)
- June 2015 (1)
- January 2015 (1)
- September 2014 (2)
- August 2014 (1)
- July 2014 (4)
- June 2014 (9)
- May 2014 (2)
- April 2014 (1)
- March 2014 (1)
- February 2014 (1)
- December 2013 (1)
- November 2013 (5)
- October 2013 (5)
- September 2013 (5)
- August 2013 (5)
- July 2013 (5)
- June 2013 (2)
- May 2013 (2)
- April 2013 (4)
- March 2013 (5)
- February 2013 (2)
- January 2013 (3)